Thermal Fluid System Expansion Tank Design
By Robert A. Damiani, Technical Director, Radco Industries
An essential component of thermal systems utilizing liquid phase thermal fluids is an expansion tank. This type of thermal system requires an expansion tank for two reasons. First, the expansion tank serves as the safe outlet for the increase in thermal fluid volume due to thermal expansion. Second, the expansion tank provides a mechanism for venting water, incondensibles, degradation by-products and entrained air during startup and operation. Of equal concern in thermal systems operating at 300°F or above is a design that will maintain the temperature of the thermal fluid/atmosphere interface below 300°F to minimize fluid oxidation.
In liquid phase thermal systems there are three types of expansion tank designs:
1. Baffled tanks
2. Straight Leg Tanks
3. Flow Through (or “Surge” Tanks)Surge tank designs essentially are tanks serving as a receiver for thermal fluid from the user with the main circulating pump drawing thermal fluid from the bottom of the tank for return to the heater. This design offers no oxidation protection and in fact increases oxidation due to the aeration of the thermal fluid in the tank itself. This is a poor design for extended thermal fluid use but does provide excellent thermal system venting capabilities during startup and extended operation.The baffled tank has three chambers or baffles. As the thermal fluid is heated, expansion of the fluid occurs from the first chamber into the second, and then into the main tank. In a properly sized expansion tank, when a thermal system is properly filled with cold thermal fluid there will be a significant level of fluid in the main baffle. With this type of design, thermal fluid in the main baffle rarely, if ever, co-mingles with hot fluid in the primary thermal system heat transfer loop because of inherent system fluid pressures. The fluid in the main baffle is significantly cooler than in the other baffles, forming a thermal blanket over the fluid in the primary thermal system heat transfer loop materially decreasing degradation of the thermal fluid due to oxidation.
As a general rule, in liquid phase thermal systems the expansion tank volumes should be approximately 26% – 30% of the total estimated volume of thermal fluid in the thermal system. The properly sized expansion tank should be approximately 1/4 full at startup temperatures and 3/4 full at operating temperatures.As the thermal system is brought up to operating temperature, the straight leg design allows the expanded thermal fluid to enter directly into the bottom of the main expansion tank by means of a small diameter pipe bypassing the flow-through valves under the expansion tank on the pump suction side of the tank Since the expansion tank is located at the highest point of the thermal system, the bulk of the thermal fluid will flow directly to the heater. Similar inherent fluid pressures as seen in the baffled tank keep thermal fluid in the expansion tank from co-mingling freely with fluid in the primary thermal system heat transfer loop. This type of design does not offer the same oxidation protection as the baffled design and, depending on system temperatures, an inert gas blanket may be required. Excellent thermal system venting may be accomplished by configuring the main line tank bypass valving to run through the expansion tank.
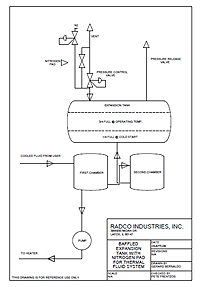